TOOLING & PRODUCTION
A part is only as good as your process will allow. Thermoflex utilizes state of the art equipment for every stage of the manufacturing process. Our processes are highly automated and highly controlled from our headquarters outside Chicago. This allows us to develop parts more quickly than our competitors and bring parts to market with all possible speed while still ensuring the quality that our customers demand.
Vertically Integrated Tooling & Machining
Taking control of your upstream processes means time and money saved for both Thermoflex and our customers. This philosophy has led Thermoflex to build a CNC and machining department capable of producing almost all of our own tools. Keeping our processes in-house ensures a smooth flow from design into production.
Texturing & Graining
Thermoflex works with a wide range of OEM approved partners to ensure that the graining of our parts integrates flawlessly into a car’s interior. Thermoflex will use single or multiple grain patterns to bring out the best in our parts and our customer’s vehicles.
8,000,000
mats shipped last year
534
stat title
Production
All of our parts are produced through the process of injection molding. Injection molding is a process that offers unparalleled repeatability and process stability, while achieving an even part thickness across the piece.
Thermoflex has made a significant investment in our injection molding machines. Over the last several years, we have continued to grow our overall production capacity without sacrificing our versatility. At present, our overall production capacity and machine capabilities remain unmatched in our industry.
Post Production
Our state of the art machinery is not limited to our CNC and Injection Molding machines. Our facility is equipped with state of the art automated packaging equipment that can minimize the labor necessary to meet any packaging needs our customers may have.
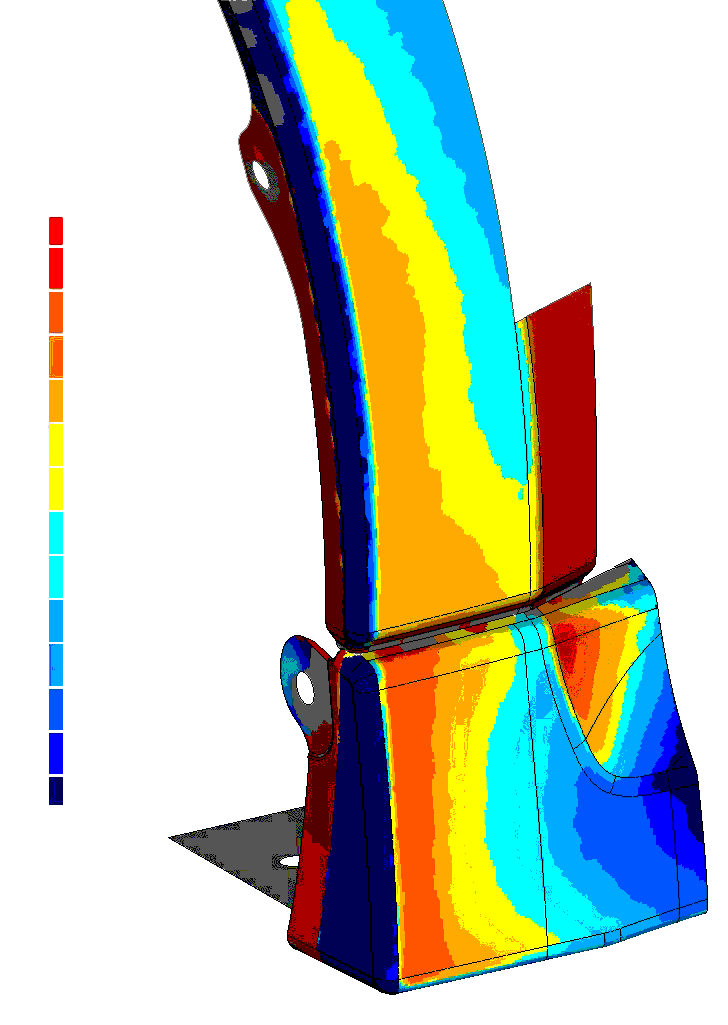