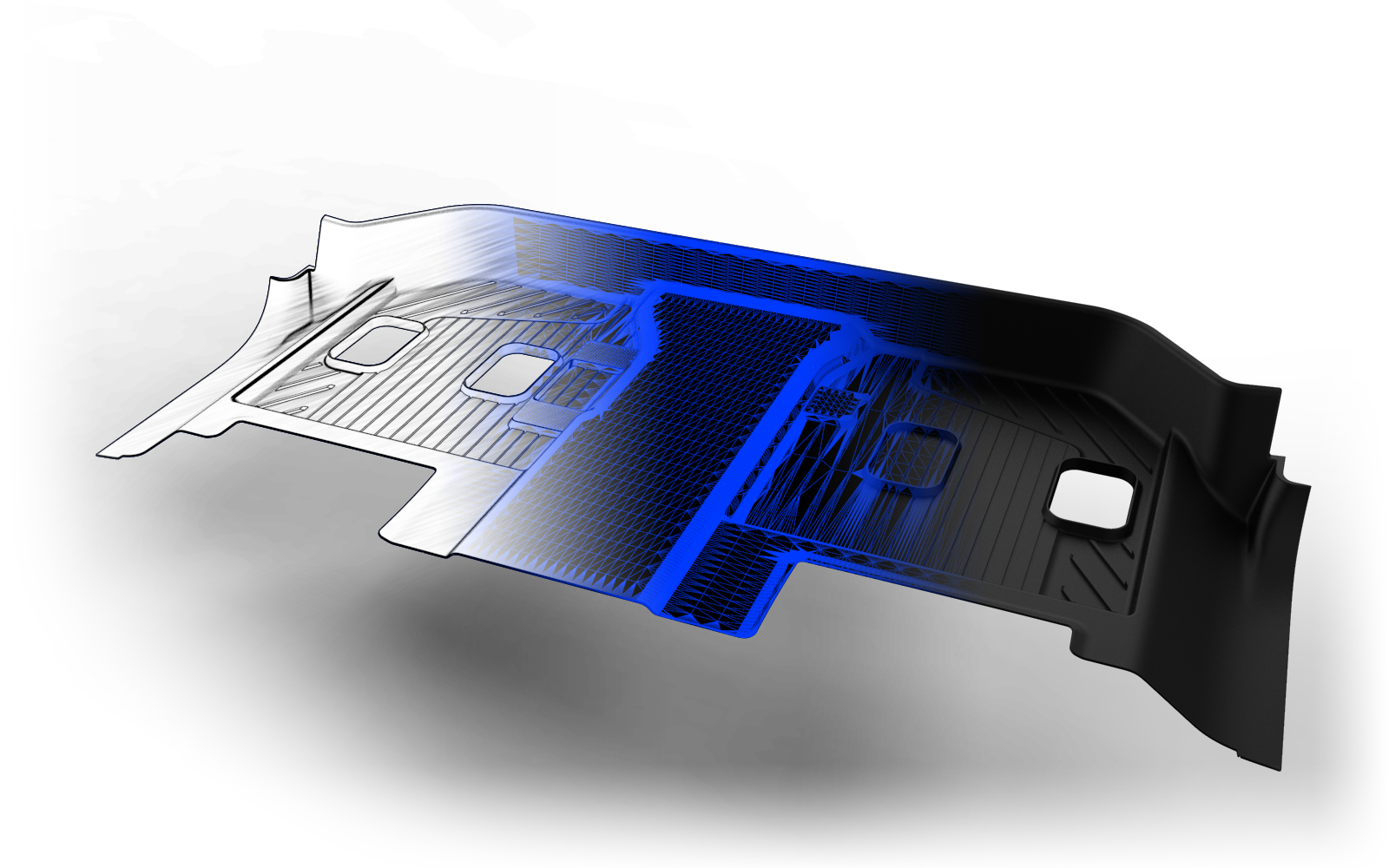
Design Process
Our designs are what distinguish Thermoflex from the competition. Automotive accessories cannot be designed and developed in a vacuum: for a part to look and function in the desired fashion, the design of the whole vehicle must be taken into consideration
Design Planning
We believe that each part and each design must be an entity unto itself. For this reason, we delve into each design from a fresh mind-set and combine our design concepts with our vast array of engineering experience to apply our designs to the specific vehicle for which it is intended. From the very beginning, both the aesthetic and functional needs of the finished parts are carefully considered.
Because each project is approached from a fresh mindset, we remain undeterred when a project requires something that has never been achieved before. Our design and engineering expertise has lead us to such innovations as the 2nd color molded logo, the integrated grommet retention device, and the injection molded carpet mat.
Design Engineering
Once a design has been developed, that design is then translated into 3D CAD models. Our CAD systems allow us to verify the dimensions of the part and produce fully rendered 3D models so that final design approval can be received. Thermoflex supports the following CAD systems:
- Creo
- Catia v5
- NX5, NX6, NX7 (Unigraphics)
- AutoCAD
- IDEAS
- Geomagic Qualify, Studio
Benifits
Design Engineering
Once a design has been finalized, Thermoflex can utilize our in-house rapid prototyping facilities to produce a prototype part in the span of days, not weeks.
Digital Materials
While we can produce a hard part similar to a traditional stereolithography, our next-generation machinery allows us to utilize the latest generation of “digital materials”.
Flexible
These materials can mimic the feel and flexibility of a wide range of materials, allowing a prototype part that will form and flex to the area just like the final part will.
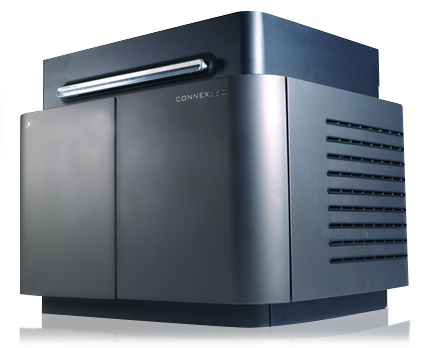
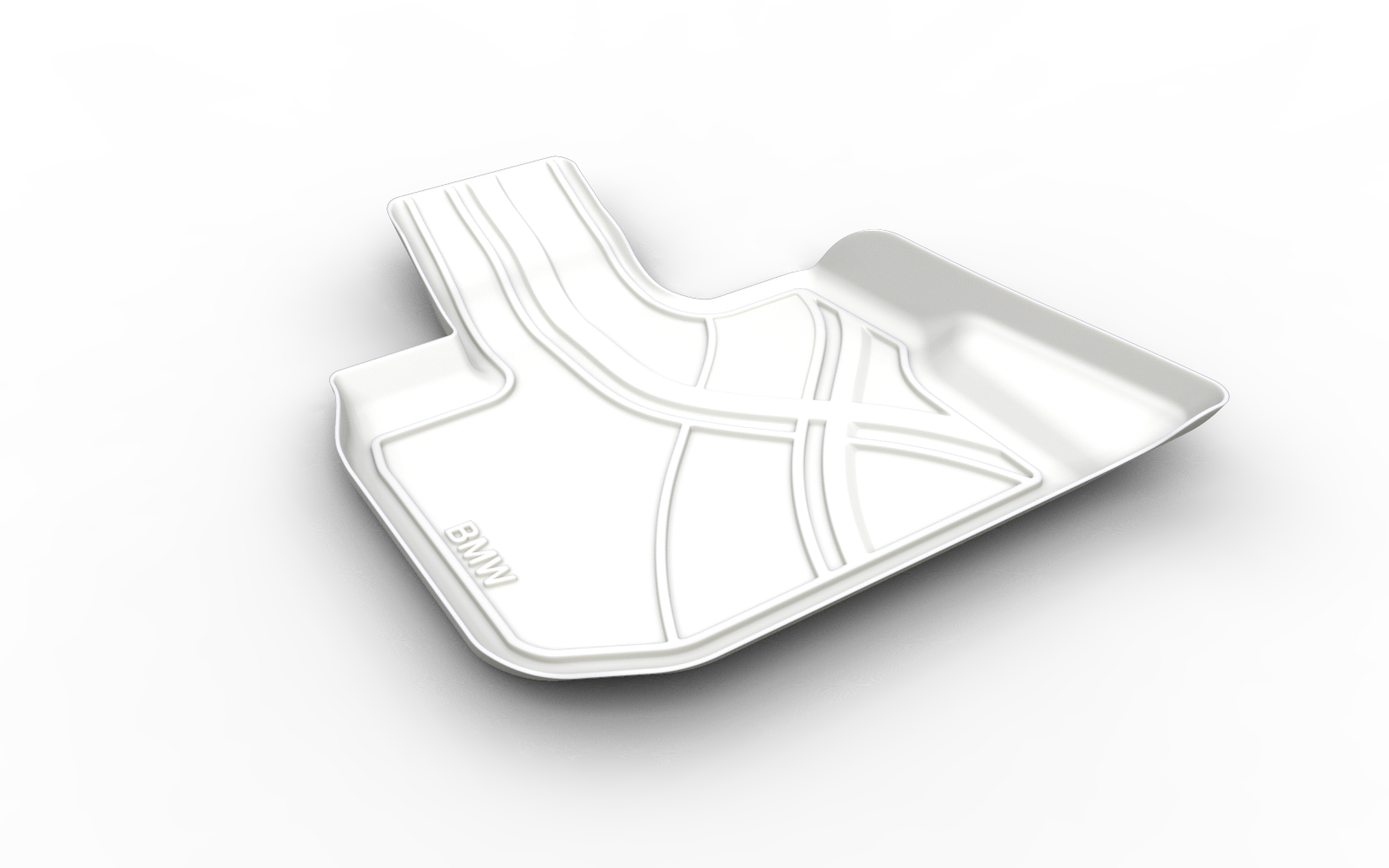
15,000+
New Part Designs
100+
Prototypes Created